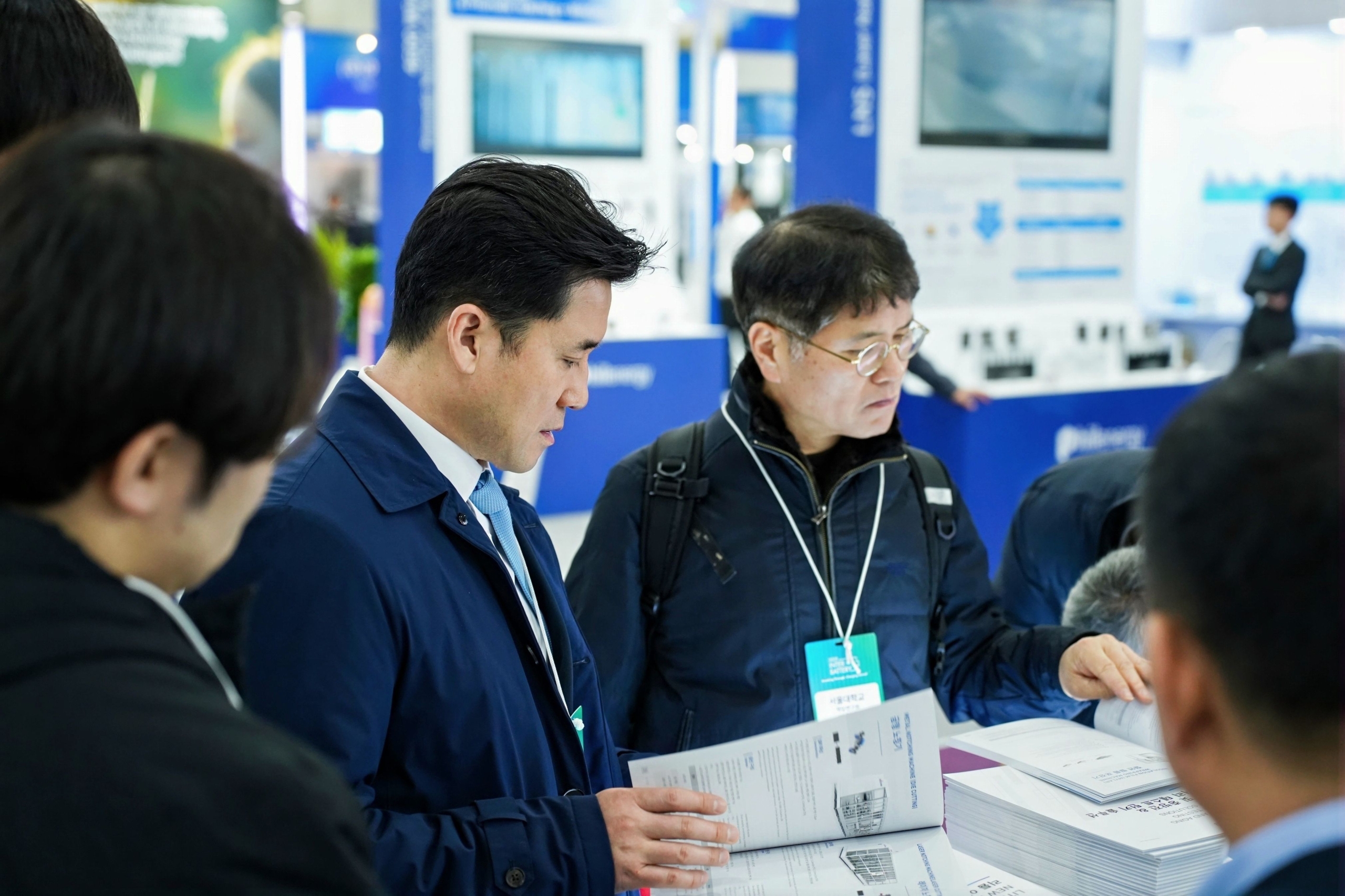
From 5 to 7 March 2025, the global battery industry’s flagship event, InterBattery 2025, opened at Seoul’s COEX Exhibition Center. As South Korea’s largest and most influential battery expo, this year’s show brought together 358 leading companies and more than 30,000 industry experts to explore breakthroughs in battery technology and energy transition trends.
Lead Intelligent Equipment (hereafter referred to as LEAD) made a splash with its “full value chain + full lifecycle” intelligent manufacturing solutions for new energy. LEAD showcased core smart‐manufacturing technologies across EV batteries, energy storage batteries, solid‐state batteries and back‐end testing, drawing widespread attention.
Series of Debuts Ignite the Show
At this year’s exhibition, LEAD unveiled two major assembly‐line solutions for the first time: a blade‐cell assembly line and a large‐capacity containerized energy‐storage‐cell assembly line. The blade‐cell line employs an all‐new assembly process, achieving an end‐to‐end yield of 98.5%—an industry‐leading figure. The large‐capacity line, designed for containerized energy‐storage cells, delivers 20 PPM throughput while offering high compatibility, stability and intelligence, representing exceptional value.
Within LEAD’s cylindrical‐cell assembly portfolio, the cylindrical cell anode bottom welding machine also stole the spotlight. By harnessing an innovative laser‐welding technique, it achieves “zero” auxiliary time, raises laser utilization above 90% and secures a welding yield in excess of 99.8%. Its specialized structural design further reduces footprint by 57% and cuts the required number of laser generators by 83%.
Recognition for Technological Innovation
LEAD’s turneky solution for all‐solid‐state battery manufacturing remained a focal point. Its technical team delivered a keynote entitled “All‐Solid‐State Batteries: Key Equipment and Technological Innovations,” detailing recent breakthroughs and comprehensive solutions. The presentation dissected core process advances—dry mixing and coating, wet ultrathin‐film coating, film transfer, insulating‐frame preparation and full‐cell stacking—all of which have excelled in solid‐electrode fabrication. LEAD’s lithium‐metal anode fabrication and surface‐modification techniques, alongside its in‐development high‐efficiency densification technology, sparked in‐depth exchanges with senior executives from several leading battery makers.
High‐Performance Products Earn Praise
In the formation and capacity‐grading segment, LEAD’s intelligent manufacturing solution achieved a recovery efficiency of up to 90%, with outstanding precision and consistency, earning market acclaim. Its cell cycle‐testing system, featuring a response time of ≤ 2.5 ms, a minimum pulse width of 10 ms and test accuracy of ≤ ± 0.02% FS, also drew high praise from clients.
As a global leader in new‐energy intelligent manufacturing solutions, LEAD remains committed to redefining industry boundaries through technological innovation. Its “full value chain + full lifecycle” offerings—from materials innovation and process upgrades to cycle testing—span the entire battery‐manufacturing chain, empowering customers to achieve dual enhancements in intelligent manufacturing and green, low‑carbon operations.
Amid the global energy‐transition wave, LEAD will continue deepening collaborative innovation with partners worldwide, leveraging its smart‐manufacturing engine to shape energy’s future and accelerate the realization of a zero‑carbon world.